Automatic Cooling Bed
Introduction
An automatic cooling bed is a vital piece of equipment in rolling mills, designed to handle and cool down hot rolled products, such as bars, rods, and sections, as they exit the rolling mill. This system ensures uniform cooling, proper alignment, and efficient handling of the finished products, contributing significantly to the quality and efficiency of the rolling process.
Functionality
The primary function of an automatic cooling bed is to receive the hot rolled products from the rolling mill and facilitate their controlled cooling. Key operations include:
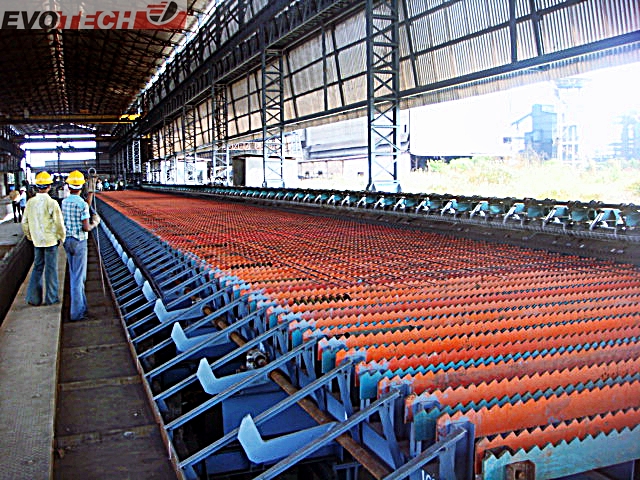
1. Uniform Cooling: The cooling bed ensures even cooling of the hot rolled products to prevent warping and internal stresses.
2. Alignment and Layering: It aligns and layers the products systematically, aiding in subsequent handling and processing.
3. Transport Mechanism: The cooling bed moves the products along its length, allowing sufficient time for the metal to cool down to a manageable temperature.
4.Discharge: After cooling, the products are discharged and transferred to storage or further processing units.
Design Considerations
- Structure:Composed of a robust framework to support the weight and thermal stress of hot rolled products.
- Cooling Mechanism: Utilizes natural air cooling or enhanced methods such as water sprays or air blowers to accelerate the cooling process.
- Transport System: Includes walking beams, rakes, or moving slats to transport the products across the cooling bed uniformly.
- Automation:Equipped with sensors and automated controls to manage the movement, alignment, and discharge of products efficiently.
Benefits of Automatic Cooling Beds
- Enhanced Product Quality:Ensures uniform cooling, reducing residual stresses and warping, which enhances the structural integrity of the final product.
- Operational Efficiency:Automation and systematic handling increase throughput and reduce the need for manual intervention.
- Flexibility:Capable of handling various sizes and shapes of rolled products, making it adaptable to different production requirements.
- Safety:Automated systems minimize the need for direct human contact with hot materials, improving workplace safety.
Operational Aspects
- Integration:Integrated seamlessly into the rolling mill line, positioned to receive products immediately after the final rolling stand.
- Real-Time Control: Automated systems control the speed and movement of products, ensuring synchronized operation with the rolling mill output.
- Maintenance: Regular maintenance of the mechanical components and cooling systems is crucial for consistent performance and longevity.
- Safety Protocols:Incorporates safety features such as emergency stop mechanisms and protective guards to ensure the safety of operators.
Applications
- Steel and Metal Rolling Mills: Used for cooling and handling various hot rolled products, including bars, rods, and structural sections.
- Construction Material Production: Essential for producing high-quality steel bars and rods used in construction.
- Automotive Industry:Cools and aligns metal sections used in automotive manufacturing.
- Metal Fabrication:Prepares metal products for further processing and fabrication.
Conclusion
The automatic cooling bed is an indispensable component in modern rolling mills, ensuring the efficient and uniform cooling of hot rolled products. Its design focuses on operational efficiency, product quality, and safety, making it a critical investment for any rolling mill operation. As technology advances, automatic cooling beds continue to evolve, offering enhanced performance and adaptability to meet the growing demands of the metalworking industry.