Centering Device in Steel Rolling Mills
Introduction
A centering device is specialized equipment used in steel rolling mills to ensure accurate alignment and positioning of steel billets, slabs, or other materials before they enter the rolling stands. It plays a critical role in optimizing material handling, enhancing operational efficiency, and improving product quality during the rolling process.
Functionality:
The centering device serves several essential functions in the steel rolling mill:
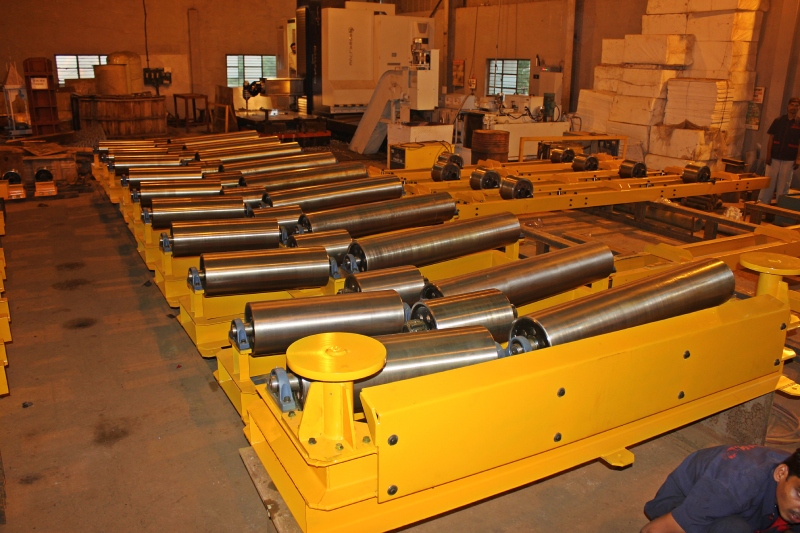
- Alignment and Positioning: Aligns incoming billets or slabs to ensure they enter the rolling stands in a centralized and uniform manner, minimizing lateral movement and misalignment.
- Improving Entry into Rolls: Prepares the material for entry into the rolling stands by adjusting its position and orientation, facilitating smooth and consistent feeding.
- Reducing Setup Time: Streamlines the setup process by automating the alignment and centering of materials, reducing manual adjustments and setup time between production runs.
- Enhancing Product Quality: Ensures uniform deformation and rolling of the material by maintaining consistent alignment, resulting in improved dimensional accuracy, surface finish, and mechanical properties of the rolled products.
Design and Components:
- Adjustable Rollers or Guides: Utilizes adjustable rollers, guides, or pneumatic actuators to manipulate and position the material accurately before it enters the rolling stands.
- Control System: Equipped with PLC-based control systems and sensors to detect material position and adjust the centering device accordingly.
- Drive Mechanism: Powered by motors and gearbox systems to provide precise movement and positioning of the material, ensuring optimal alignment.
Benefits of Centering Device:
- Operational Efficiency: Improves overall mill efficiency by reducing setup time, minimizing material handling errors, and optimizing material flow through the rolling process.
- Enhanced Productivity: Facilitates continuous operation by automating the material alignment and centering process, reducing downtime and increasing throughput.
- Consistent Product Quality:Ensures consistent alignment and entry into the rolling stands, resulting in uniform product dimensions, surface finish, and mechanical properties.
- Safety and Reliability:Enhances workplace safety by reducing the risk of material jams, misfeeds, and equipment damage during the rolling operation.
Operational Aspects:
- Integration into Rolling Mill Line:Positioned strategically at the entry point of the rolling stands to optimize material handling and streamline production flow.
- Maintenance:Regular inspection and maintenance of rollers, guides, and control systems are essential to ensure reliable operation and extend equipment lifespan.
Applications:
- Steel Rolling Mills:Essential in hot and cold rolling processes for steel billets, slabs, and sheets to ensure accurate alignment and consistent rolling.
- Non-ferrous Metal Rolling:Applied in aluminum, copper, and other metal rolling processes to optimize material handling and improve product quality.
Conclusion
The centering device is a critical component in steel rolling mills, enabling precise alignment and positioning of materials before they undergo rolling. Its advanced design, automation capabilities, and integration with rolling mill operations contribute to enhancing productivity, optimizing material handling, and maintaining consistent product quality in steel and metal manufacturing industries. As technology advances, centering devices will continue to evolve to meet the increasing demands and challenges of modern rolling mill operations.