Twin Channel for Rolling Mills
Introduction
In steel rolling mills, a twin channel (also known as twin-path or double-path) plays a critical role in the continuous casting process of molten metal into solid billets or blooms. It serves as a crucial intermediary stage between the ladle and the molds, where the molten steel is guided, divided, and shaped into multiple strands for subsequent solidification. The twin channel ensures efficient and controlled flow of liquid steel, enhancing productivity and quality in the steel manufacturing process.
Functionality
The trough tilter serves several essential functions in the steel manufacturing process:
- Ladle Tilting: Tilts ladles containing molten metal to pour the liquid metal into molds or casting stations. This process facilitates controlled pouring to achieve precise filling and minimize splashing.
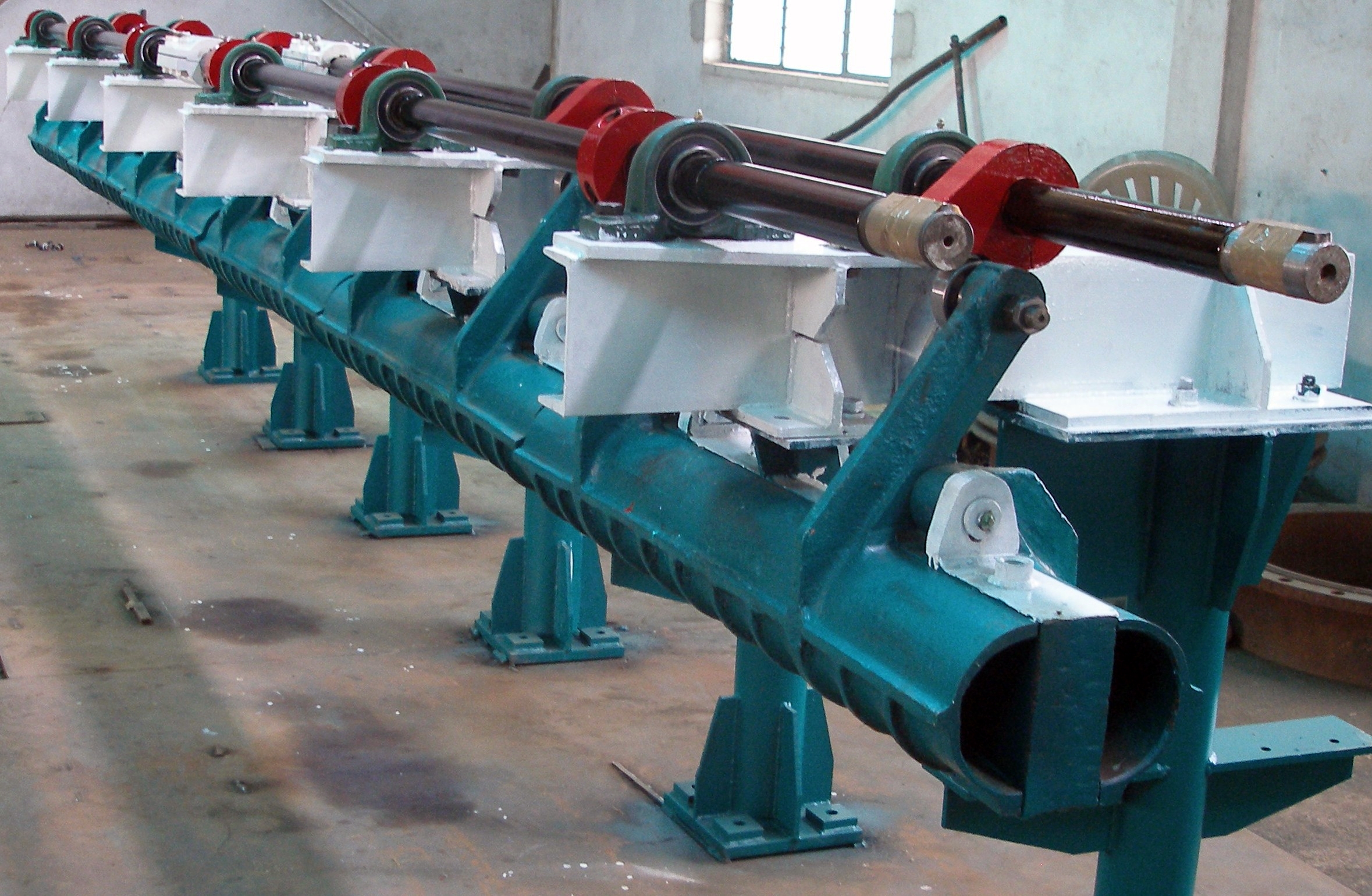
Key Features and Benefits
- Dual Flow Control:Facilitates simultaneous casting of multiple steel strands (typically two or more), optimizing throughput and production efficiency.
- Segregation and Distribution:Divides the molten metal stream from the ladle into separate channels or paths, ensuring uniform distribution and filling of molds.
- Temperature Control:Maintains consistent molten metal temperature during casting to promote solidification and prevent defects in the final billets or blooms.
- Versatility:Designed to handle various steel grades, sizes, and configurations of billets or blooms, accommodating diverse customer requirements.
- Continuous Operation:Supports continuous casting operations, enabling uninterrupted flow of molten metal and minimizing downtime between casting cycles.
Components of Twin Channel
- Tundish:Receives molten metal from the ladle and distributes it evenly to multiple pouring nozzles or outlets.
- Pouring Nozzles:Guides the molten metal into the twin channels, controlling the flow rate and direction to ensure uniform distribution into the molds.
- Twin Channels:Consist of refractory-lined pathways or troughs that carry the molten metal from the pouring nozzles to the molds, facilitating solidification.
- Cooling System:Incorporates water-cooled elements or jackets along the twin channels to regulate and cool the molten metal, aiding in solidification.
- Automation and Control:Includes PLC (Programmable Logic Controller) and sensors for automated operation, monitoring of flow rates, temperatures, and casting parameters.
Operational Workflow
- Molten Metal Transfer:Molten steel is transferred from the ladle to the tundish, where it is prepared for distribution to the twin channels.
- Divided Flow:The tundish divides the molten metal into multiple streams, each directed through separate pouring nozzles into the twin channels.
- Casting Process:Molten metal flows through the twin channels, filling the molds where it solidifies into billets or blooms of specified dimensions.
- Solidification and Extraction:Solidified billets or blooms are extracted from the molds and prepared for further processing, such as hot rolling or subsequent heat treatment.
- Maintenance and Inspection:Regular maintenance of refractory linings, cooling systems, and automation components ensures reliable operation and extends equipment lifespan.
Applications in Steel Rolling Mills
- Billet and Bloom Casting: Producing semi-finished steel products used in construction, automotive, and industrial applications.
- High-Quality Steel Production: Ensuring uniformity and quality in the casting process for specialty steel grades and alloys.
- Productivity Enhancement: Optimizing casting efficiency and throughput to meet increasing demand for steel products.
Twin channels are essential in continuous casting operations for:
Conclusion
The twin channel is a vital component in steel rolling mills, facilitating efficient and controlled casting of molten metal into solid billets or blooms. EVO TECH's advanced twin channel systems integrate robust design, precise flow control, and automation technologies to enhance productivity, quality, and operational efficiency in steel manufacturing. By optimizing the casting process, EVO TECH continues to support steel producers worldwide in delivering high-performance steel products to diverse industries and markets.