Pinch Roll and Tail Breaker for Rolling Mill
Introduction
Pinch rolls and tail breakers are essential components in rolling mills, designed to handle and control the movement of steel billets, blooms, or slabs through various stages of the rolling process. They play critical roles in ensuring smooth material flow, preventing slippage, and facilitating efficient operation of the rolling mill.
Pinch Roll
Functionality
Pinch rolls serve several key functions in the rolling mill:
- Material Feeding: Pinch rolls guide and feed the incoming material (billets, blooms, or slabs) into the rolling stands with precise alignment and speed control.
- Tension Control: They maintain tension on the material to prevent slack and ensure continuous and uniform feeding into the rolling mill.
- Speed Regulation:Pinch rolls help regulate the speed of the material entering the rolling stands, synchronizing it with the mill’s operation for optimal rolling conditions.
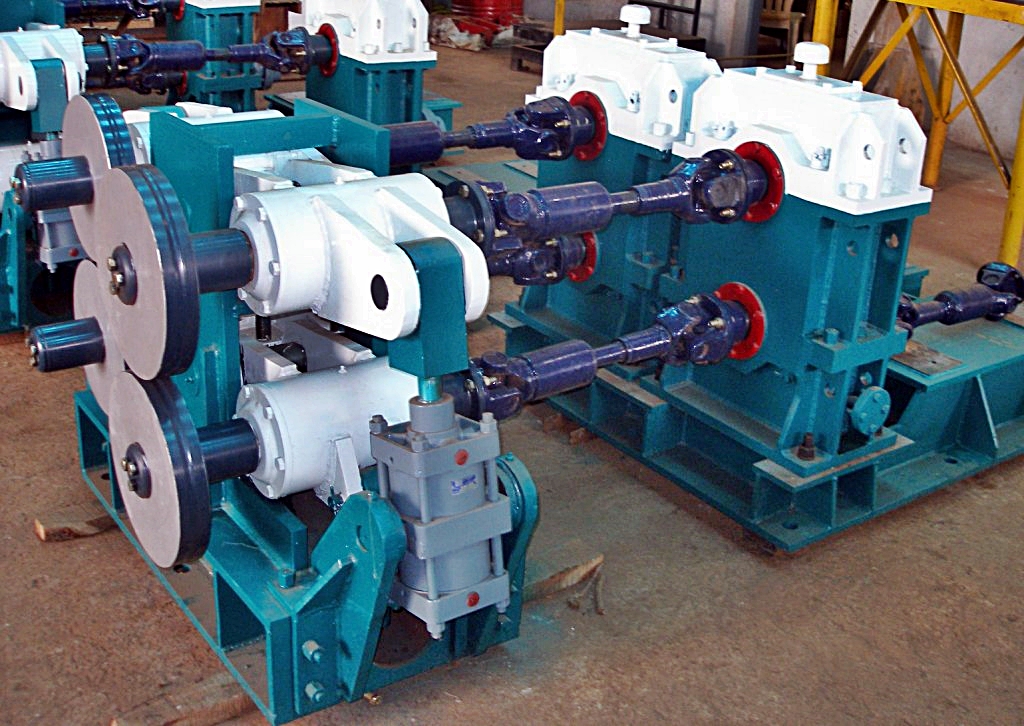
Design Considerations for Pinch Roll
- Rolls Construction: Pinch rolls are equipped with specially hardened and polished rolls to minimize wear and ensure smooth material handling.
- Drive System: They are driven by powerful motors and gear systems capable of providing precise speed and torque control.
- Adjustability: Adjustable settings allow operators to fine-tune the pressure and gap between the rolls, accommodating different sizes and shapes of the material.
- Cooling Mechanism:Some pinch rolls incorporate cooling systems to dissipate heat generated during operation, maintaining optimal working temperatures.
Tail Breaker
Functionality
Tail breakers are critical for controlling the discharge of material from the rolling mill:
- Material Separation:Tail breakers separate the finished product (e.g., rolled bars, rods, or sheets) from the trailing end of the material being rolled.
- Acceleration Control:They control the acceleration of the discharged material to prevent damage and ensure smooth transition to the next processing stage.
- Cooling and Alignment: Tail breakers may assist in aligning and cooling the discharged material before it moves to further processing or storage.
- Emergency Stop: Similar to pinch rolls, tail breakers have emergency stop capabilities to halt material flow in case of emergencies or operational issues.
Design Considerations for Tail Breaker
- Mechanical Design: Tail breakers are designed with robust mechanical components capable of handling the weight and speed of discharged materials.
- Control System:Integrated with the mill’s automation system to synchronize material discharge with the rolling process and downstream operations.
- Safety Features:Includes safety mechanisms such as sensors and emergency stop buttons to ensure safe operation and prevent accidents.
Benefits of Pinch Roll and Tail Breaker
- Enhanced Productivity:Ensure continuous and controlled material handling, optimizing production efficiency in the rolling mill.
- Quality Assurance:Maintain consistent tension, alignment, and handling of the material, crucial for producing high-quality rolled products with uniform dimensions and properties.
- Operational Efficiency:Minimize downtime and operational disruptions by facilitating smooth material flow and transition between rolling stages.
- Safety and Reliability: Improve workplace safety by preventing material slippage or mishandling, ensuring reliable and efficient mill operation.
Operational Aspects
- Integration:Pinch rolls and tail breakers are strategically positioned within the rolling mill line to optimize material handling and processing efficiency.
- Maintenance:Regular inspection and maintenance of pinch rolls and tail breakers are essential to ensure optimal performance and extend their operational lifespan.
- Automation and Control:Integrated with advanced automation systems to monitor and adjust parameters such as speed, tension, and alignment in real-time.
- Environmental Considerations:Efforts to reduce energy consumption and waste in every aspect of operation contribute to sustainable and efficient mill practices.