Hot Billet Charging Mechanism:
Hot billet charging is a crucial process in modern steelmaking and metal forging industries. It involves feeding preheated metal billets directly from a furnace into a downstream process, such as rolling or forging, without allowing them to cool down significantly. This method offers several advantages over conventional cold charging:
- Energy Efficiency: By preheating the billets to temperatures close to the processing temperature, hot billet charging reduces the energy required to reheat them from ambient temperatures. This results in lower energy consumption and overall cost savings.
- Improved Process Control: Hot billet charging helps maintain consistent temperatures throughout the production process. This consistency is critical for achieving uniform material properties and dimensional accuracy in the final product.
- Increased Throughput: Since the billets are already at a high temperature, they can be fed into downstream equipment immediately, reducing downtime and increasing overall production efficiency.
- Environmental Benefits: Lower energy consumption translates into reduced greenhouse gas emissions and environmental impact, aligning with sustainable manufacturing practices.
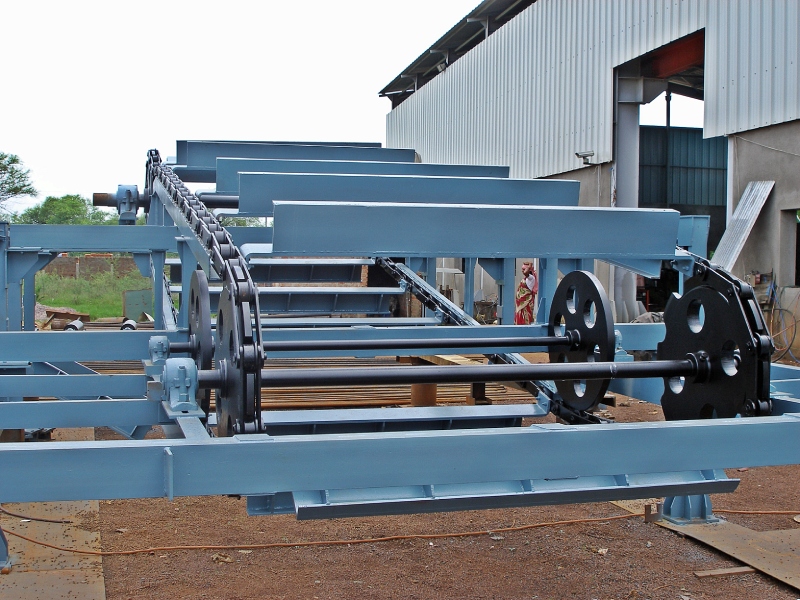
The hot billet charging mechanism typically involves a conveyor system that transfers the heated billets from the reheating furnace to the rolling or forging mill. Special attention is paid to maintaining the temperature of the billets during transfer to ensure they remain within the optimal processing range.
Key considerations for implementing hot billet charging include the design of the conveyor system, heating technology used in the furnace, and integration with existing production processes. Proper planning and engineering are essential to maximize the benefits of this method while ensuring safety and operational reliability.
In conclusion, hot billet charging is a proven technique that enhances efficiency, reduces costs, and improves the environmental footprint of metal production processes. It is widely adopted in steel mills and forging plants worldwide to achieve higher throughput and product quality.