Rocking Runner for Blast Furnace Operations
Introduction:
The rocking runner is a crucial component in blast furnace operations, used to guide molten iron and slag from the furnace to the casting areas or ladles. Its design and functionality ensure the safe and efficient transport of these materials, which is essential for maintaining continuous production and preventing operational disruptions.
Functionality:
The primary purpose of the rocking runner is to channel the molten materials away from the blast furnace tap hole to subsequent processing or storage areas. This process involves several key actions:
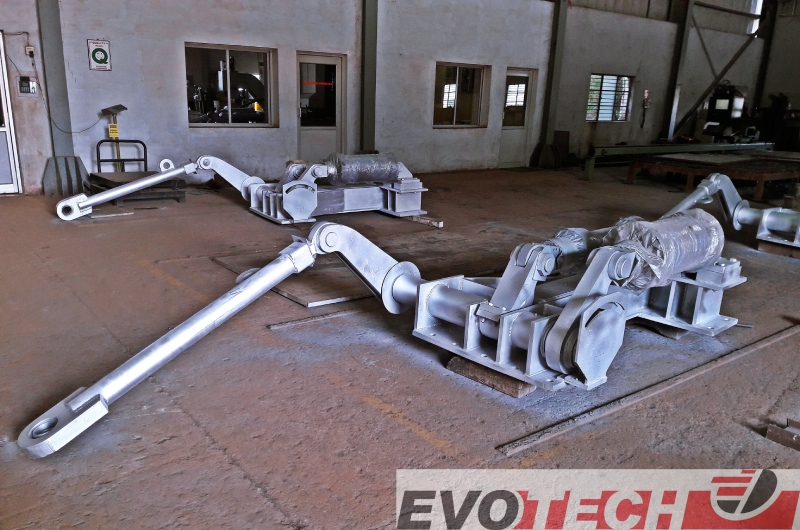
- Collection: Molten iron and slag are tapped from the blast furnace and enter the runner system.
- Guidance: The rocking runner directs these molten streams to the desired locations, typically casting beds or ladles for further processing.
- Tilting Mechanism: The "rocking" action refers to the runner's ability to tilt or oscillate, which helps control the flow and direction of the molten materials.
Design Considerations:
- Material and Construction: The runner must be made from high-temperature resistant materials, such as refractory-lined steel, to withstand the extreme conditions and corrosive nature of molten iron and slag.
- Tilting Mechanism: The design includes hydraulic or mechanical systems that enable the runner to rock or tilt, allowing precise control over the flow direction and rate.
- Durability: The construction must be robust to endure continuous thermal cycling and mechanical stresses, with provisions for regular maintenance and replacement of worn-out parts.
Benefits of the Rocking Runner:
- perational Efficiency: The rocking mechanism allows operators to control the flow of molten materials accurately, reducing spillage and wastage.
- Safety: By guiding the molten iron and slag safely, the rocking runner minimizes the risk of accidents and enhances overall workplace safety.
- Product Quality: Controlled flow helps in maintaining the quality of the cast products by ensuring consistent material feed and reducing contamination.
- Flexibility: The tilting capability allows the runner to adapt to different operational requirements, such as directing materials to multiple destinations or handling varying flow rates.
Operational Aspects:
- Automation: Modern rocking runners are often equipped with automated control systems that adjust the tilt angle based on real-time monitoring of the flow conditions.
- Maintenance: Regular inspection and maintenance are crucial to ensure the runner's longevity and performance. This includes checking the refractory lining, hydraulic systems, and structural integrity.
- Monitoring: Continuous monitoring of the molten material flow and runner condition helps in early detection of potential issues, allowing for timely interventions.
Conclusion:
The rocking runner is an indispensable component in blast furnace operations, ensuring the efficient and safe transport of molten iron and slag.