Multi-Gravity Separator (MGS)
Introduction:
A Multi-Gravity Separator (MGS) is an advanced piece of equipment used in mineral processing to separate and concentrate fine and ultrafine particles based on differences in their specific gravity. This technology is particularly effective for recovering valuable minerals from low-grade ores and tailings, enhancing overall yield and efficiency in mining operations.
Functionality:
The MGS operates on the principle of enhanced gravity separation, which combines the effects of centrifugal force and conventional shaking table motion to improve the separation efficiency of fine particles. The main components and process steps include:

- Feed Introduction: The slurry, containing a mixture of minerals and water, is fed into the separator.
- Centrifugal Action: The MGS employs a rotating drum or a series of cones, creating a centrifugal force that enhances the gravitational effect on particles.
- Shaking Motion: The separator’s surface undergoes a shaking motion, facilitating the stratification of particles based on their specific gravity
- Separation Zones: Particles with higher specific gravity are forced to the outer edges and are collected separately from the lighter particles, which remain closer to the center.
Design Considerations:
- Rotating Drum or Cones: The core element of the MGS, designed to generate high centrifugal forces for effective separation.
- Adjustable Parameters: The rotational speed, shaking frequency, and angle of inclination can be adjusted to optimize the separation process for different types of ores and particle sizes.
- Materials of Construction: High-wear and corrosion-resistant materials are used to construct the separator to ensure longevity and reliability in harsh operating conditions.
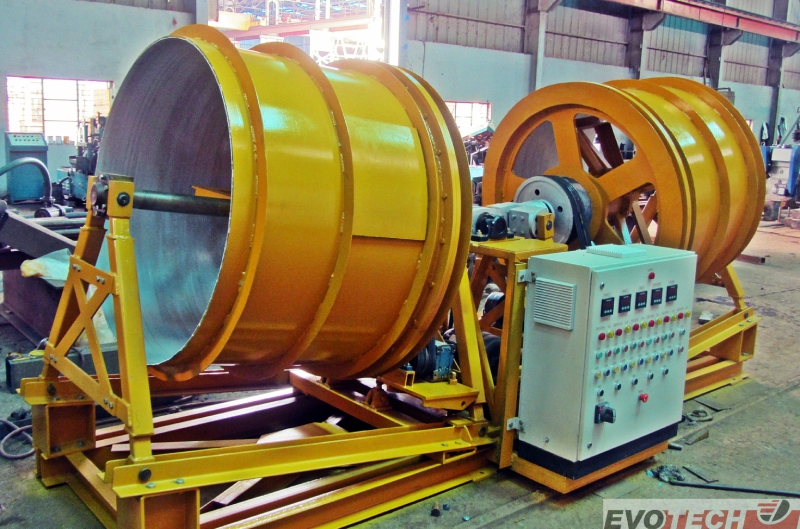
Benefits of Multi-Gravity Separators:
- High Recovery Rates: Capable of recovering fine and ultrafine particles that are often lost in traditional gravity separation methods.
- Enhanced Efficiency: Provides higher separation efficiency due to the combined effects of centrifugal force and shaking motion, which enhances particle stratification.
- Versatility: Can be used for a wide range of minerals, including precious metals, base metals, and industrial minerals.
- Reduced Environmental Impact: By recovering more valuable minerals from tailings and low-grade ores, the MGS reduces the need for extensive mining and processing, leading to lower environmental impact.
Operational Aspects:
- Feed Preparation: The feed slurry must be well-prepared, with appropriate particle size distribution and pulp density, to achieve optimal separation.
- Parameter Optimization: Continuous monitoring and adjustment of operational parameters are essential to maintain high separation efficiency and adapt to variations in feed composition.
- Maintenance: Regular maintenance of the rotating drum/cones, feed mechanisms, and discharge systems is crucial to ensure consistent performance and prevent downtime.
- Integration: The MGS can be integrated into existing mineral processing circuits, enhancing the overall efficiency and recovery rates of the operation.
Applications:
- Mineral Processing: Widely used in the mining industry for the recovery of precious metals (gold, silver), base metals (lead, zinc), and industrial minerals (tungsten, graphite).
- Environmental Remediation: Effective in recovering valuable materials from mining tailings and waste, reducing environmental impact and reclaiming land.
- Recycling: Used in recycling operations to separate and recover valuable metals from electronic waste and other scrap materials.
Conclusion:
The Multi-Gravity Separator (MGS) is a powerful and versatile tool in the field of mineral processing, offering significant advantages in the recovery of fine and ultrafine particles. Its ability to enhance separation efficiency and recover valuable minerals from low-grade ores and tailings makes it an essential component in modern mining operations. As technological advancements continue, the MGS will likely see further improvements in performance and applicability, contributing to more sustainable and efficient mineral processing practices.