Horizontal and Vertical Loopers in Rolling Mills
Introduction
Horizontal and vertical loopers are essential components in rolling mills, used to control and manage the continuous flow of material, such as coils or strips, between rolling stands and other processing units. They play a critical role in maintaining tension, improving product quality, and optimizing the efficiency of the rolling process.
Horizontal Looper
Functionality:
Horizontal loopers serve several key functions in the rolling mill:
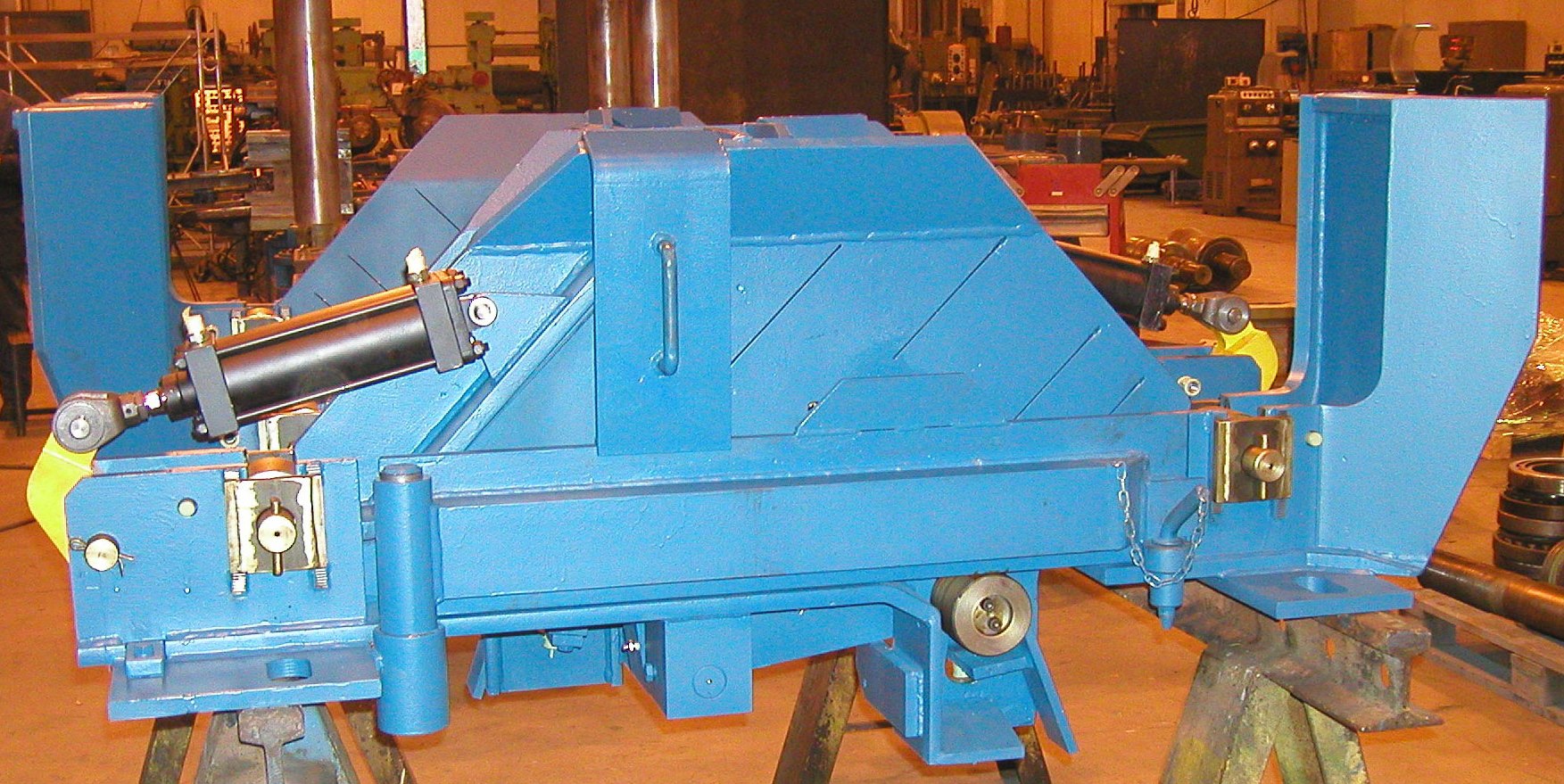
- Tension Control: Absorb and release excess strip length to maintain consistent tension throughout the rolling process, preventing material breakage and ensuring smooth operation.
- Accumulation and Buffering: Accumulate material during mill operation and buffer the strip between rolling stands, allowing continuous rolling without interruptions.
- Strip Tracking:Assist in guiding the strip through the rolling stands while adjusting to variations in strip speed and thickness, ensuring uniform product dimensions.
Design and Components:
- Looping Pit or Table: Consists of a horizontal platform or pit where the strip accumulates and forms loops as it passes through the rolling mill.
- Looping Mechanism: Utilizes movable rollers or hydraulic cylinders to adjust the height and length of the strip loop, controlling tension and facilitating smooth material flow.
- Drive Systems: Powered by motors and gearbox systems to adjust loop size and position based on rolling speed and strip thickness variations.
Vertical Looper
Functionality:
Vertical loopers perform similar functions to horizontal loopers but are used in different orientations and applications:
- Tension Control:Manage vertical loops of material between different levels in the rolling mill or between processing units, maintaining tension and preventing material buckling or stretching.
- Space Optimization:Suitable for mills with limited horizontal space, as vertical loopers can handle material accumulation in a compact vertical footprint.
- Integration with Processing Units: Coordinate with downstream equipment such as coilers, shears, and inspection stations to ensure smooth material transfer and processing.
Design and Components:
- Vertical Looping Mechanism:Uses hydraulic or mechanical systems to adjust the height and length of the vertical loop, accommodating varying strip speeds and processing requirements.
- Support Structure:Features a robust framework and support beams to withstand the weight and tension of the material during looping and handling.
Benefits of Horizontal and Vertical Loopers:
- Improved Product Quality: Ensure consistent tension and material handling, resulting in uniform product dimensions, surface finish, and mechanical properties.
- Operational Efficiency: Facilitate continuous rolling operations by absorbing variations in strip speed and thickness, reducing downtime and increasing mill throughput.
- Safety and Reliability:Minimize risks of material breakage or mishandling, enhancing workplace safety and reducing operational disruptions.
- Flexibility:Adapt to different rolling processes and product specifications, accommodating various types of materials and production requirements.
Operational Aspects:
- Integration into Rolling Mill Line:Positioned strategically between rolling stands, coilers, and other processing units to optimize material flow and production efficiency.
- Maintenance:Regular inspection and maintenance of rollers, drive systems, and hydraulic components are essential to ensure reliable operation and extend equipment lifespan.
Applications:
- Steel and Metal Rolling Mills:Used in hot and cold rolling processes for steel coils, sheets, and strips, as well as in non-ferrous metal production for aluminum, copper, and other alloys.
- Continuous Casting Lines:Applied in continuous casting operations to manage and control the flow of molten metal before solidification into billets or slabs.
Conclusion
Horizontal and vertical loopers are critical components in rolling mills, enabling efficient material handling, tension control, and process optimization. Their advanced design, integration with automation systems, and ability to handle varying production demands contribute to enhancing productivity, ensuring product quality, and maintaining safe operations in steel and metal manufacturing industries. As technology advances, loopers will continue to evolve to meet the evolving needs and challenges of modern rolling mill operations.