EVO TECH and MINITEC Partnership for Energy Optimizing Furnaces (EOF)
EVO TECH has entered into a strategic agreement with MINITEC, Brazil, to manufacture, supply, install, commission, and provide subsequent repairs for Energy Optimizing Furnaces (EOF) in India. This collaboration aims to bring advanced, efficient, and cost-effective steel production solutions to the Indian market.
- EOF Proper: The main furnace unit where the melting and refining process occurs
- Scrap Preheater (if specified): Preheats scrap material using waste heat, improving energy efficiency.
- Waste Heat Recovery System (if specified): Captures and reuses waste heat from the furnace, enhancing overall energy efficiency.
- Gas Cleaning System: Ensures emissions are cleaned to meet environmental standards.
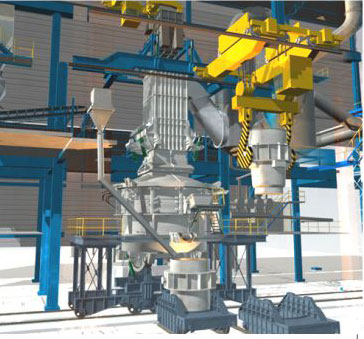
- Combined Oxygen Blowing: Utilizes both submerged and atmospheric oxygen blowing to enhance efficiency
- Maximum Utilization of Sensible Heat: Efficiently uses heat generated from reactions for preheating scrap and other processes.
- Scrap Preheating: Uses sensible heat from waste gases to preheat scrap, improving energy efficiency.
- High Scrap Utilization: Capable of incorporating up to 40% scrap in the charge, reducing costs.
- Submerged Tuyeres: Special tuyeres for submerged oxygen blowing, ensuring long life and efficiency.
- ficient Wet Dedusting System: Reduces dust emissions, ensuring environmental compliance.
- Deslagging and Second Slag Formation: Efficient removal of slag and formation of secondary slag during the blow process.
- High Purity Liquid Steel: Produces steel with very low levels of phosphorus and sulfur.
- Low Noise Levels: Designed to operate with minimal noise.
- High Productivity: able of up to 45 heats per day, ensuring high production rates.
Conclusion:
Combining these features, the EOF provides a lower cost of production than other routes while offering great flexibility in the metallic charge mix. This partnership between EVO TECH and MINITEC ensures the delivery of advanced, efficient, and cost-effective steel production solutions in India, positioning the EOF as a premier choice for modern steel manufacturing.