SINTER PLANT:
EVOTECH's collaboration with MINITEC to provide turnkey solutions for sinter plants signifies a strategic partnership aimed at enhancing the efficiency and performance of sinter plant operations. Here are the key aspects and potential benefits of this collaboration:
1) Turnkey Solutions:
- Design and Engineering: Comprehensive design and engineering services to optimize sinter plant layouts and processes.
- Equipment Supply: Provision of all necessary equipment for the sinter plant, ensuring compatibility and optimal performance.
- Installation and Commissioning: Complete installation and commissioning services, ensuring that the plant is operational and meets performance targets.
- Automation and Control: Advanced automation and control systems to enhance process efficiency and ensure consistent product quality.
- Training and Support: Training programs for plant personnel and ongoing technical support to ensure smooth operation and maintenance.
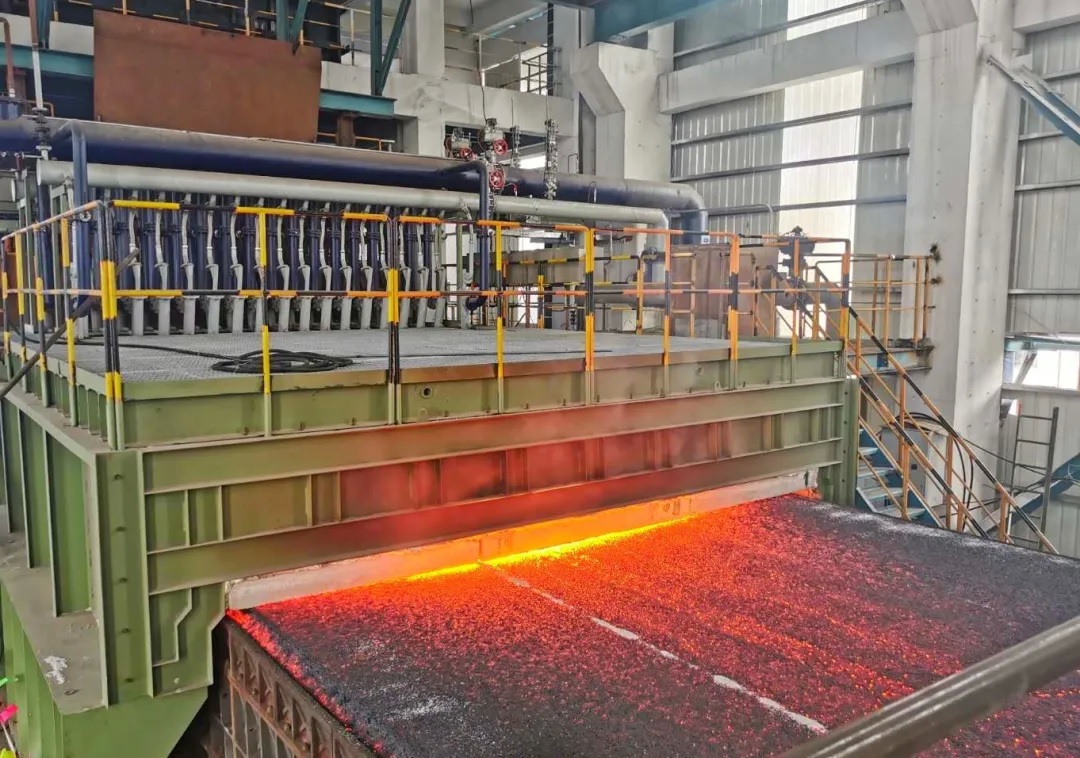
- State-of-the-Art Technology: Incorporation of the latest technologies and innovations to improve sintering processes.
- Sustainable Practices: Focus on energy-efficient and environmentally friendly technologies to reduce emissions and operational costs.
3) Project Management:
- End-to-End Management: Handling of the entire project lifecycle from concept to completion, ensuring timely delivery and adherence to budget.
- Quality Assurance: Rigorous quality control measures to ensure that all components and systems meet the highest standards/
Benefits of the Collaboration:
- Efficiency Gains: Enhanced process efficiency through optimized design and advanced automation, leading to increased productivity and reduced operational costs.
- Quality Improvement: Consistent production of high-quality sinter, meeting the stringent requirements of blast furnace operations.
- Cost Savings: Reduction in energy consumption and maintenance costs through the use of efficient technologies and high-quality equipment.
- Environmental Compliance: Implementation of sustainable practices and technologies to minimize environmental impact, helping plants comply with environmental regulations.
- Risk Mitigation: Reduced risk through a single point of responsibility for the entire project, ensuring seamless integration and operation.
Applications:
- New Sinter Plants: Full-scale design, construction, and commissioning of new sinter plants.
- Upgrades and Retrofits: Modernization of existing sinter plants to improve performance, efficiency, and environmental compliance.
Sinter plants agglomerate iron ore fines (dust) with other fine materials at high temperature, to create a product that can be used in a blast furnace. The final product, a sinter, is a small, irregular nodule of iron mixed with small amounts of other minerals. The process, called sintering, causes the constituent materials to fuse to make a single porous mass with little change in the chemical properties of the ingredients. The purpose of sinter are to be used converting iron into steel. Sinter plants, in combination with blast furnaces, are also used in non-ferrous smelting. About 70% of the world's primary lead production is still produced using the sinter plant–blast furnace combination,[1] and this combination was formerly often used in copper smelting Main feed into a sinter plant is base mix, which consists of iron ore fines, coke fines and flux (limestone) fines. In addition to base mix, coke fines, flux fines, sinter fines, iron dust (collected from plant de-dusting system & ESP) and plant waste are mixed in proportion (by weight) in a rotary drum, often called mixing and nodulizing drum. Calcined lime is used as binder of the mixed material along with water (all in particular proportion by weight) to form feed-sinter of about 5 to 7 mm in size. This sinter globules are fed to sintering machine and burnt there-in to produce blast furnace feed sinter.
Conclusion:
The collaboration between Evotech and Minitec leverages the strengths and expertise of both companies to deliver comprehensive turnkey solutions for sinter plants. This partnership is poised to offer significant improvements in efficiency, quality, and sustainability, making it a valuable proposition for the iron and steel industry.
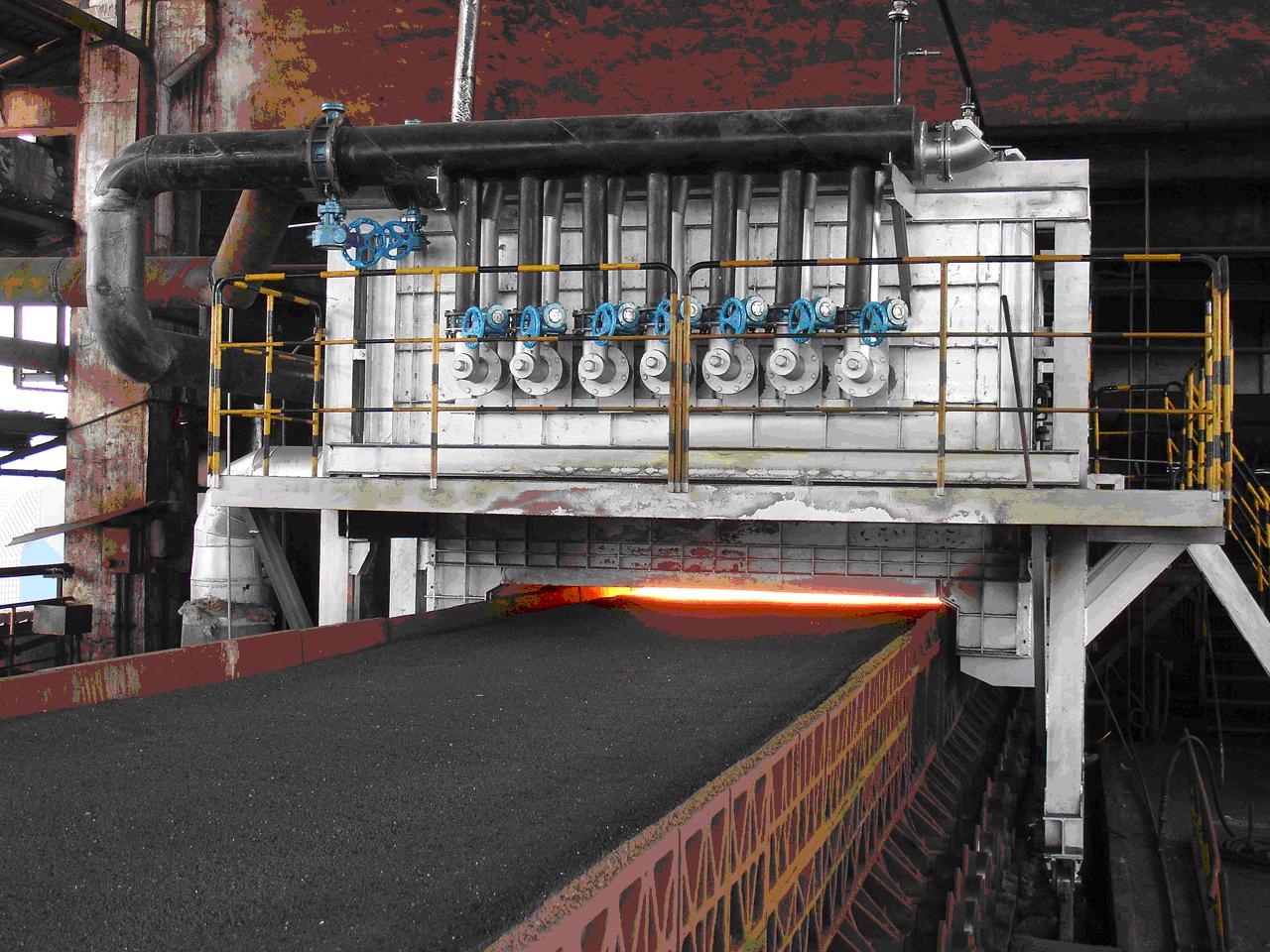
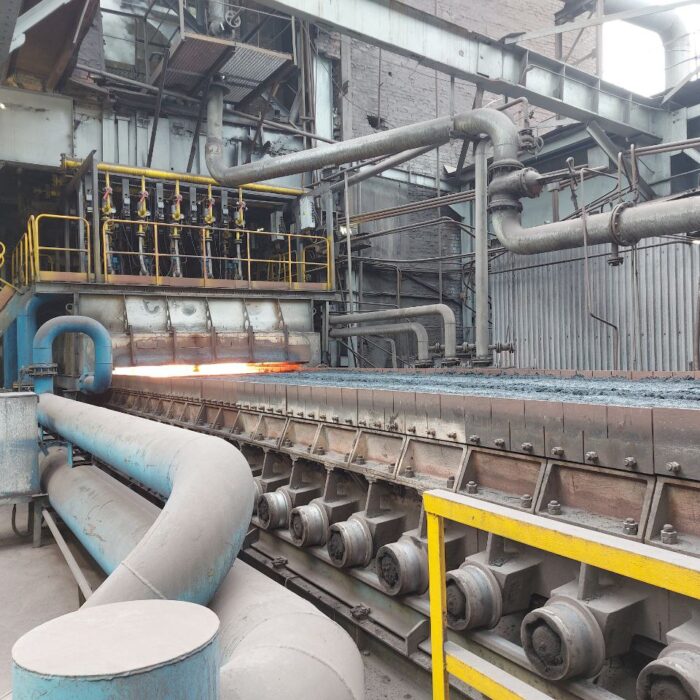