Pinch Rolls for Rail Mill
Introduction
Pinch rolls are integral components in rail mills, essential for guiding and controlling the movement of steel billets or blooms through various stages of the rolling process. They play a crucial role in maintaining proper alignment, tension, and speed control of the material as it progresses through the mill, ensuring consistent quality and dimensional accuracy of the final rail products.
Functionality:
Pinch rolls perform several critical functions in the rail mill operation:
- Material Guidance:Pinch rolls guide the steel billets or blooms into the rolling stands, ensuring they enter with precise alignment and orientation.
- Tension Control:They maintain tension on the material to prevent slippage and ensure uniform feeding into the rolling stands, which is crucial for consistent reduction and shaping.
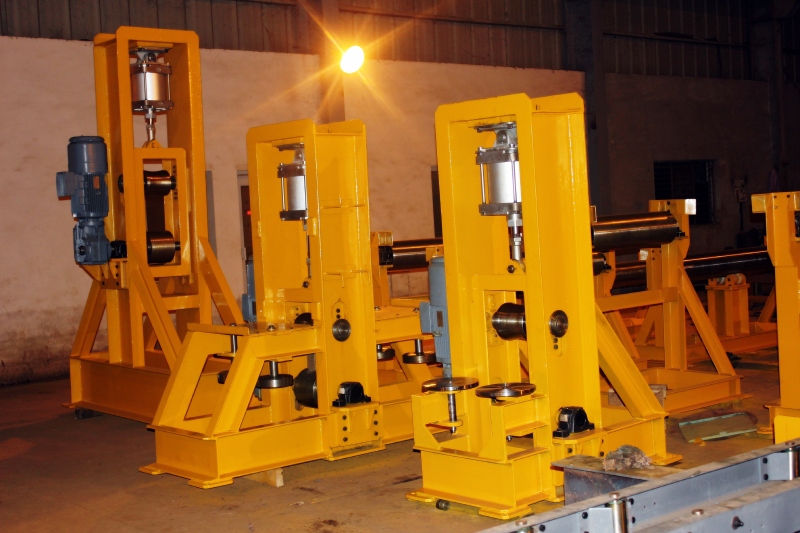
Design Considerations:
- Rolls Construction: Pinch rolls are typically equipped with hardened and polished rolls to minimize wear and ensure smooth material handling.
- Drive System: They are driven by powerful motors and gear systems capable of providing precise speed and torque control.
- Adjustability: Adjustable settings allow operators to fine-tune the pressure and gap between the rolls, accommodating different sizes and shapes of the material.
- Cooling Mechanism: Some pinch rolls incorporate cooling systems to dissipate heat generated during operation, maintaining optimal working temperatures.
Benefits of Pinch Rolls:
- Enhanced Productivity: Ensure continuous and controlled feeding of material into the rolling mill, optimizing production efficiency.
- Quality Assurance: Maintain consistent tension and alignment, which is crucial for producing rails with uniform dimensions, mechanical properties, and surface finish.
- Safety: Provide emergency stop capabilities to protect personnel and equipment from potential accidents or damage.
- Operational Efficiency: Synchronize material flow with the rolling process, minimizing downtime and improving overall mill performance.
Operational Aspects:
- Integration: Positioned at the entry of the rolling stands, pinch rolls seamlessly integrate into the rail mill’s production line.
- Maintenance: Regular inspection and maintenance of pinch rolls ensure optimal performance and extend their operational lifespan.
- Automation and Control: Integrated with automation systems to monitor and adjust parameters such as speed, tension, and roll pressure in real-time.
- Environmental Considerations: Efforts to reduce energy consumption and waste in every aspect