Continuous Shear for Rolling Mills
Introduction
In the steel manufacturing process, continuous shears play a crucial role in the operation of rolling mills. These machines are designed to cut steel bars, rods, or other profiles into desired lengths continuously and accurately. Continuous shears are integral to the efficiency and productivity of rolling mills, enabling seamless cutting of hot or cold material as it passes through the rolling process.
Key Features and Benefits
1. Continuous Operation:
Enables uninterrupted cutting of steel bars or profiles as they move through the rolling mill, ensuring continuous production flow.
2. High Precision Cutting:
Offers precise and accurate cutting of steel products to specified lengths, meeting tight dimensional tolerances and customer requirements.
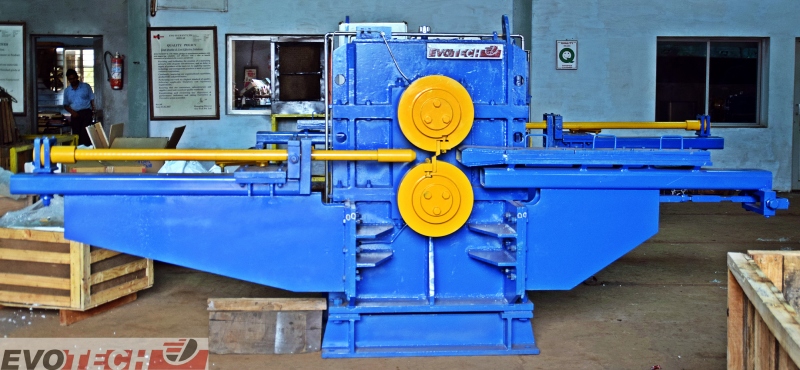
3. Versatility:
Capable of cutting a wide range of steel products, including bars, rods, angles, and channels, with varying cross-sectional shapes and sizes.
4. Integration with Rolling Mill Line:
Integrated seamlessly into the rolling mill line to synchronize cutting operations with the rolling process, minimizing downtime and optimizing throughput.
5. Automation and Control:
Equipped with advanced automation systems for programmable cutting lengths, speed synchronization, and real-time monitoring of cutting parameters.
Components of Continuous Shear
1. Cutting Mechanism:
Utilizes shear blades or rotary cutters to perform continuous cutting of steel products with precision and efficiency.
2. Conveyor System:
Transports steel bars or profiles through the shear at a controlled speed, ensuring smooth and consistent cutting operations.
3. Control System:
Includes PLC (Programmable Logic Controller) and HMI (Human-Machine Interface) for user-friendly operation, parameter setting, and monitoring of cutting processes.
4. Safety Features:
Incorporates safety guards, emergency stop systems, and sensors to protect operators and equipment during operation.
5. Maintenance and Serviceability:
Designed for ease of maintenance with accessible components and provisions for lubrication and blade sharpening.
Operational Workflow
1. Material Preparation:
Steel bars or profiles are prepared for cutting, ensuring they meet quality standards and dimensional requirements.
2. Continuous Cutting:
Steel products pass through the continuous shear, where they are cut into specified lengths based on programmed parameters.
3. Sorting and Stacking:
Cut pieces are sorted, stacked, and prepared for further processing or packaging according to customer specifications.
4. Real-Time Monitoring:
Continuous monitoring of cutting operations to ensure consistent product quality and adherence to production schedules.
5. Maintenance and Inspection:
Regular inspection and maintenance of shear blades, conveyor systems, and control components to ensure reliable performance and extended service life.
Applications in Steel Rolling Mills
Continuous shears are widely used in various types of rolling mills, including:
- Long Product Mills: Cutting of steel bars, rods, angles, and channels for construction, infrastructure, and manufacturing applications.
- Wire Rod Mills: Cutting of wire rods used in automotive, construction, and industrial sectors.
- Specialty Steel Mills: Processing of high-value steel products with specific dimensional and quality requirements.
Conclusion
Continuous shears are essential components in steel rolling mills, enabling efficient and precise cutting of steel products to meet diverse customer demands. EVO TECH's advanced continuous shear solutions integrate cutting-edge technology with robust design principles to enhance productivity, minimize waste, and ensure superior product quality in steel manufacturing. By optimizing cutting operations and maximizing operational efficiency, EVO TECH continues to drive innovations in the steel industry, supporting the production of high-quality steel products for global markets.