PRE-HEATERS / WASTE HEAT EXCHANGERS
Evo Tech has supplied a range of waste heat exchangers for many blast furnace stoves.
Functionality
Waste heat exchangers capture the residual heat from the exhaust gases of the blast furnace stoves. This heat can then be transferred to other processes or used to preheat incoming air or fuel, improving overall efficiency.
- Heat Exchanger Core: The main body where heat transfer occurs. It consists of various materials that conduct heat efficiently.
- Inlet and Outlet Ports: Allow the flow of hot exhaust gases and the medium to be heated (air, water, or other fluids).
- Fans or Blowers: Facilitate the movement of gases through the exchanger.
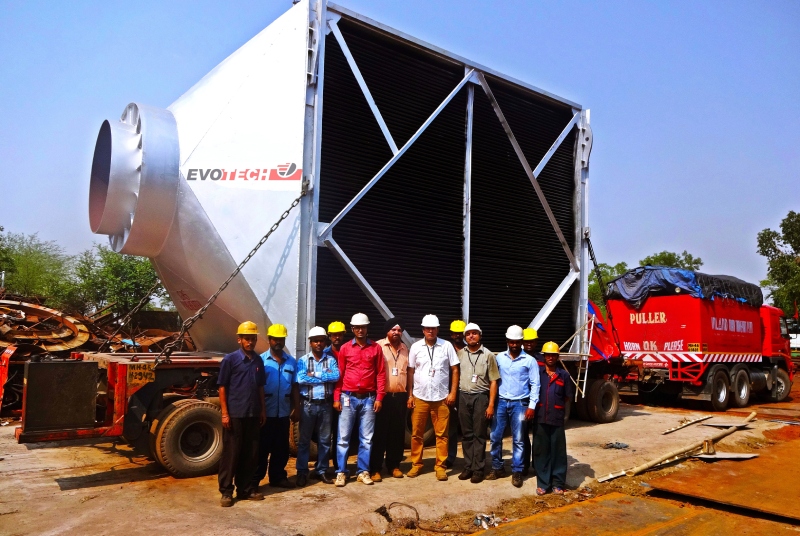
- Plate Heat Exchangers: Consist of multiple thin plates stacked together. Heat transfer occurs through the plates.
- Shell and Tube Heat Exchangers: Contain a series of tubes, with one fluid flowing through the tubes and another fluid flowing around them.
- Regenerative Heat Exchangers: Temporarily store heat in a thermal mass before transferring it to the incoming fluid.
Benefits of Waste Heat Exchangers:
- Recover and reuse heat, reducing fuel consumption.
- Preheat combustion air or fuel, enhancing the blast furnace’s performance.
2) Cost Savings:
- Lower energy bills due to reduced fuel usage.
- Decreased maintenance costs by reducing thermal stress on equipment.
3) Environmental Impact:
- Reduced carbon footprint by minimizing fuel combustion.
- Lower greenhouse gas emissions due to increased efficiency.
4) Operational Benefits:
- Improved overall process stability and control.
- Enhanced lifespan of the blast furnace and associated equipment due to optimized thermal management.
Applications in Blast Furnace Operations:
- Preheating Combustion Air: Preheating the air fed into the blast furnace stoves increases the efficiency of the combustion process.
- Steam Generation: Excess heat can be used to produce steam for other plant processes or for power generation.
- Hot Water Production: Waste heat can be used to heat water for various industrial purposes, such as cleaning or space heating.
Design Considerations:
Material Selection:
- Must withstand high temperatures and corrosive environments.
- Common materials include stainless steel, alloys, and ceramics.
Efficiency:
- High thermal conductivity materials and optimized designs ensure maximum heat recovery.
Maintenance:
- Ease of cleaning and maintaining the heat exchanger to ensure long-term performance.
- Regular inspection and replacement of worn-out components.
Integration:
- Compatibility with existing furnace infrastructure and control systems.
Conclusion:
Waste heat exchangers for blast furnace stoves are crucial for enhancing energy efficiency, reducing operational costs, and minimizing environmental impact. By effectively capturing and reusing waste heat, these systems contribute to more sustainable and economically viable industrial processes.
Combustion Air Pre-heater is a part of the Combustion Air Station and Waste Heat Recovery System for the Stove Unit. Combustion Air Pre-heater is meant for pre-heating of combustion air up to 1800C by means of utilizing the sensible heat contained in the waste gases. The Pre-heater design envisages passing of Combustion Air through the seamless hot deformed tubes welded to drilled plates while the waste gases from the stoves come into contact with the tubes at the outer surface of tubes imparting the sensible heat to the tubes and to air passing inside the tubes.
The Pre-heater is supposed to be operated at 1000mm WC pressure (max.) which means that the pressure of combustion air inside the tubes will be 1000mm WC (max.).The Pre-heater shall also be operated at elevated temperatures. The average temperature of the waste gases passing through the Waste Heat Recovery System will be 3000C, while the maximum peak short time temperature may go up to 5000C. The temperature of outlet gases leaving from the Waste Heat Recovery Unit into the Stack will be 130-1500C.The temperature of inlet BFG will be 450C and BFG outlet temperature will be 1800C. In order to save the heat imparted to BF GAS, the Pre-heater and outlet pipelines shall be insulated with a thermal insulation material
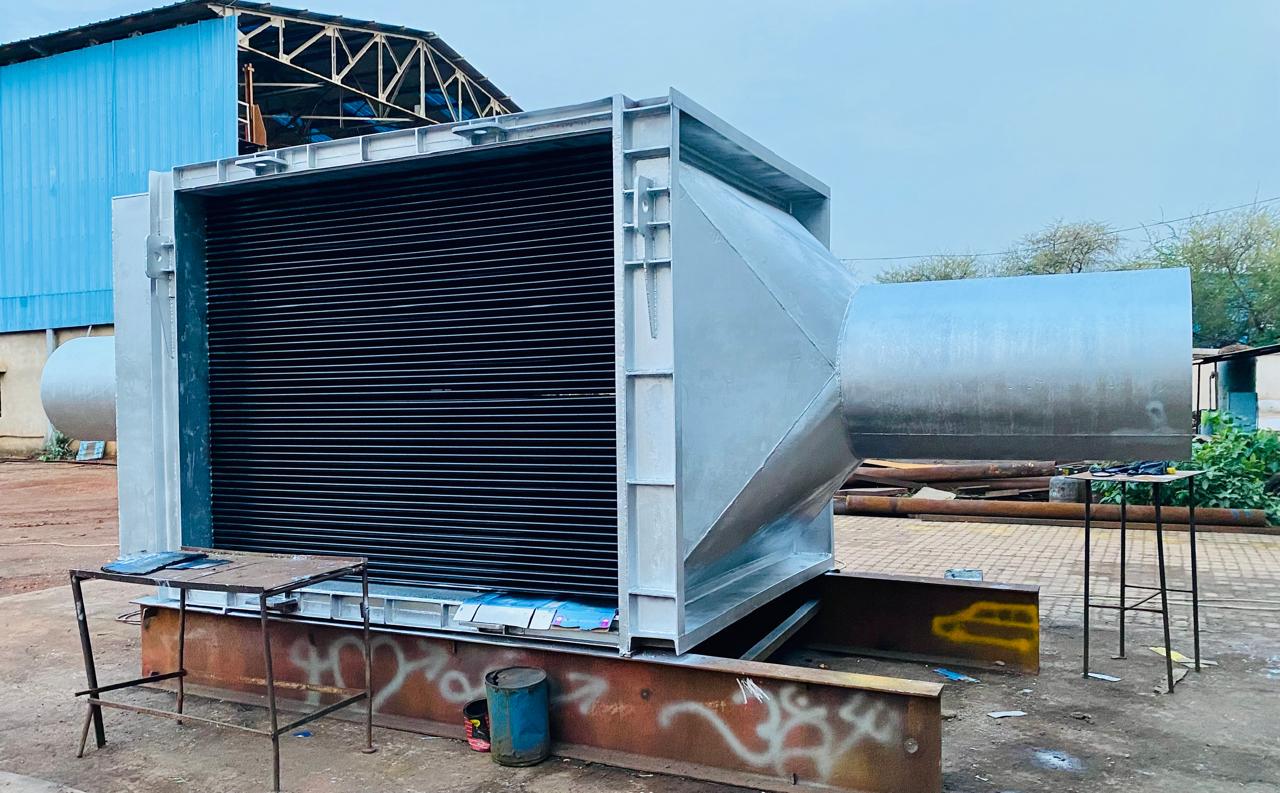