Flying Shear for Rolling Mill
Introduction
A flying shear is an essential component in modern rolling mills, designed to cut rolled metal stock (such as steel bars, rods, and sheets) to specific lengths during the continuous rolling process. This high-speed cutting device operates without interrupting the material flow, ensuring efficient production and maintaining product quality.
Functionality
Flying shears perform the crucial task of cutting the moving material to predetermined lengths while it is still in motion, preventing the need for stopping the rolling mill. Key operations include:
1. Continuous Cutting: The flying shear synchronizes with the speed of the moving material, allowing it to make precise cuts without halting the production line.
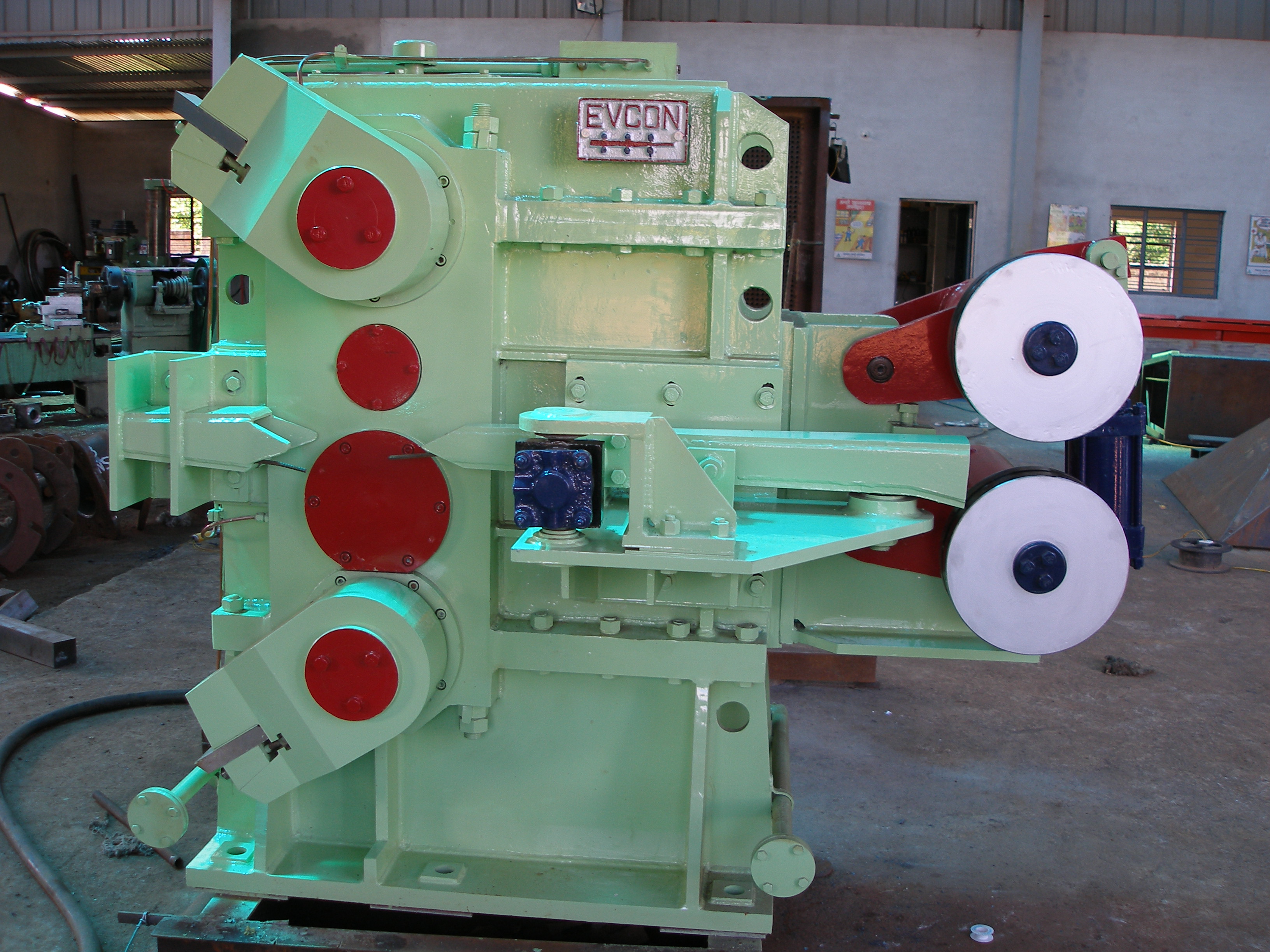
2. Adjustable Length: The system can be programmed to cut the material to various lengths, accommodating different product specifications.
3. Precision Cutting: Ensures clean, accurate cuts, which are essential for maintaining the quality and dimensions of the final product.
Design Considerations
1. Cutting Mechanism: The shear mechanism usually consists of rotating blades or guillotine-type blades designed to provide clean and precise cuts.
2. Synchronization: Advanced control systems synchronize the shear’s operation with the speed of the rolling material, ensuring timing precision.
3. Durability: Constructed from high-strength materials to withstand the mechanical stresses and high temperatures typical in rolling mills.
4. Automation: Equipped with sensors and automated controls to adjust cutting parameters in real-time, enhancing efficiency and reducing manual intervention.
Benefits of Flying Shears
1. Increased Efficiency: By cutting materials on-the-fly, the shear eliminates the need to stop the rolling mill, significantly increasing throughput and reducing downtime.
2. Enhanced Product Quality: Precise and clean cuts minimize material wastage and ensure that the final products meet strict dimensional tolerances.
3. Flexibility: The ability to cut materials to various lengths on demand makes the flying shear adaptable to different production requirements.
4. Cost Savings: Improved operational efficiency and reduced material wastage translate to cost savings for rolling mill operators.
Operational Aspects
1. Integration: The flying shear is integrated into the rolling mill’s production line, typically positioned after the finishing stands.
2. Real-Time Control:Advanced control systems monitor the rolling speed and adjust the shear’s operation to match, ensuring precise cutting.
3. Maintenance: Regular maintenance is essential to keep the cutting blades sharp and the synchronization system functioning correctly, ensuring consistent performance.
4. Safety: Safety features, such as emergency stop mechanisms and protective guards, are incorporated to protect operators and equipment.
Applications
- Steel and Metal Rolling Mills: Widely used in the production of steel bars, rods, sheets, and other metal products.
- Automotive Industry: Provides precisely cut metal sheets and components used in vehicle manufacturing.
- Construction Materials: Produces steel bars and rods of specific lengths for use in construction projects.
- Metal Fabrication: Supplies pre-cut metal pieces for various fabrication processes.
Conclusion
The flying shear is a pivotal technology in the rolling mill industry, enhancing production efficiency and product quality by allowing continuous cutting of moving materials. Its precise, automated operation reduces downtime and material wastage, making it a valuable asset in modern metal production. As rolling mill technology advances, the flying shear continues to evolve, offering even greater precision, flexibility, and efficiency to meet the demands of contemporary metalworking applications.